Ford Designed A Coronavirus Respirator - Now It's Going Into Production
Ford will begin respirator production this week at a facility in Michigan, partnering with 3M to dramatically increase the availability of vital healthcare equipment during the coronavirus pandemic. Designed by Ford, the new powered air-purifying respirator (PAPR) follows the automaker's assistance at 3M manufacturing facilities, where it helped increase production.
That, however, was only the first stage of the plan announced in late March. In addition to bringing Ford's manufacturing, purchasing, and supply chain heft to bear on 3M's lines, the automaker was also developing a PAPR design of its own. It uses components Ford is already very familiar with, albeit implemented in different ways.
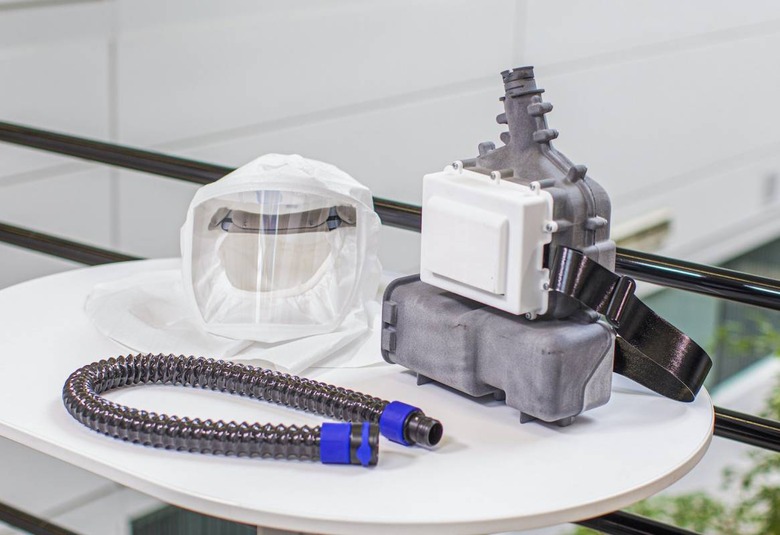
For example, the air blower system – which uses a fan and a HEPA filter to pump clean air into a hood and face shield assembly worn by healthcare professionals – is similar to that found in the ventilated seats of the F-150 pickup. It's all powered by a rechargeable battery, which Ford says can run for up to eight hours on a charge.
Altogether it took less than four weeks of development to come up with the design. Production is expected to begin on Tuesday, April 14, at the Vreeland facility near Flat Rock, Michigan. A team of approximately 90 paid UAW volunteers will be manning the line, with Ford suggesting they could produce 100,000 or more of the PAPR respirators.
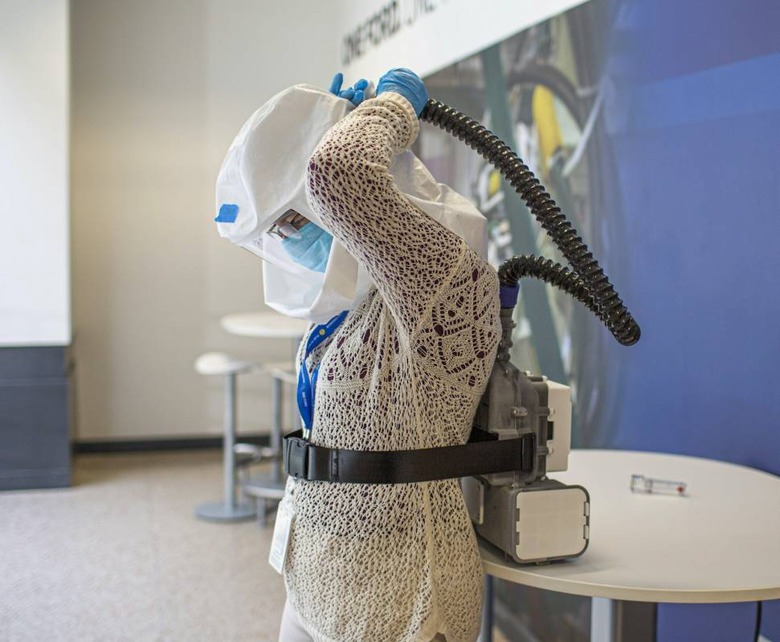
Before it can be used in healthcare settings, mind, Ford's design does need to get government approval. The automaker says it expects the respirator to be green-lit with the pending National Institute for Occupational Safety and Health (NIOSH) limited-use protocol. That could be granted by the end of April.
3M will be responsible for actual distribution, using its existing network across the US to make sure the respirators reach the right audience. "3M and Ford will donate any profits they earn from the sale of the PAPR to COVID-19 related nonprofit organizations," the two companies confirmed.
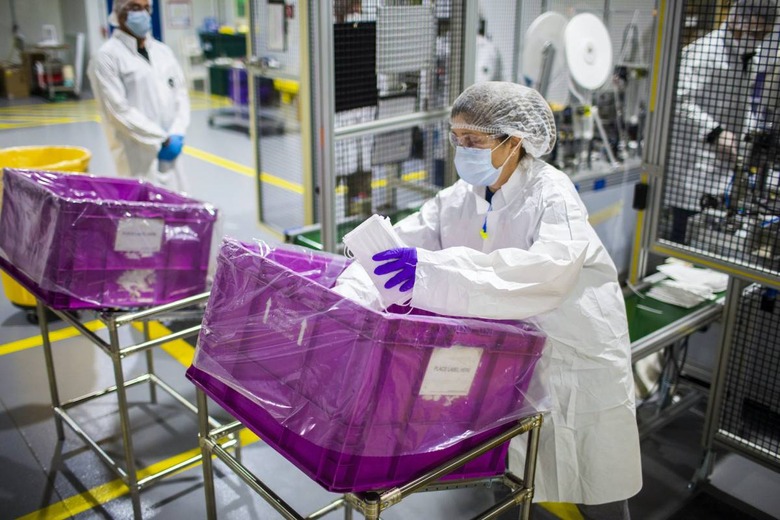
Meanwhile, Ford is also looking to have its face masks certified for medical use, having begun production of the protective equipment at the Van Dyke Transmission Plant. Eventually, the automaker says, it expects to have around 80 paid UAW volunteers building the marks, using an adapted ISO Class 8 cleanroom. Reusable gown production is also underway with airbag supplier Joyson Safety Systems, using the same material that is normally relied upon for airbags in Ford vehicles. Production there is expected to reach 75,000 gowns per week by Sunday.