This Man Has The World's First 3D Printed Eye
There are a variety of injuries and disease conditions that can result in the loss of an eye. Often, prosthetic eyes are made of glass painted to look like a natural eyeball. However, in the future prosthetic eye replacements will be made by 3D printers. Researchers at Fraunhofer Technology have made breakthroughs in 3D printing prosthetic eyes and have supplied their 3D printed eye to the first patient.
Fraunhofer researchers have developed several new technologies that improve the current manual production of individual prosthetic devices. The technology utilizes software called Cuttlefish:Eye that can create a 3D scan of the eye socket along with a color-calibrated photo of the healthy eye to create a 3D replica.
The software then utilizes a 3D printing driver to print the eye using a multicolor and multimaterial 3D printer. The result of the 3D printing technology and the scan of the healthy eye is a prosthetic that looks more realistic. Another benefit of the 3D printing technology is that while it makes a more realistic prosthetic eye, it also requires only a fraction of the time of creating them individually by hand.
Recently, a prosthetic eye created using process was given to a patient in a clinical trial conducted at Moorfields Eye Hospital London. Researchers worked on their process for four years before the first eye was used to treat a patient. Professor Mandeep Sagoo, a consultant ophthalmologist at Moorfields, says he and other researchers in the project hope the coming clinical trial will provide evidence highlighting the value of the technology. Sagoo also expects the technology to make a significant difference in the treatment for patients and to reduce waiting lists for prosthetic devices.
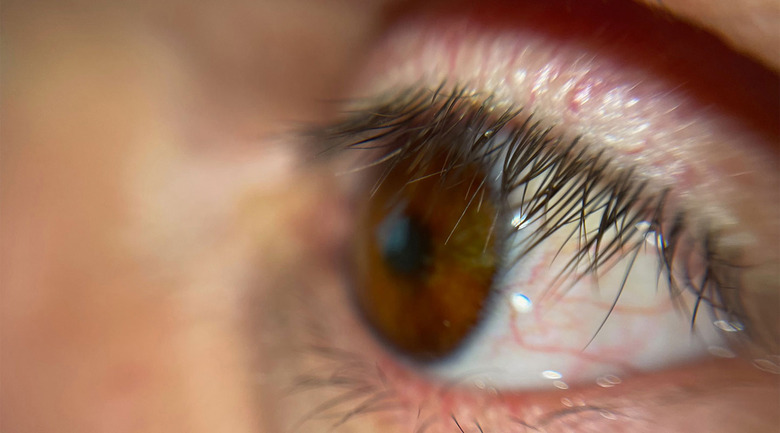
Project researchers say that various injuries and disease conditions requiring the removal of an eye impacts about three-quarters of a million people in Europe alone and over 8 million around the world. The new technology improves the creation of prosthetic eyes, which has used in the same essential manufacturing processes for decades.
One of the biggest challenges of common methods for producing this type of prosthetic is the invasive molding procedure that can be distressing enough in children that general anesthetic is required. Once the molding process is over, current production methods utilize time-consuming handcrafted work creating several months of waiting before the eye is available. Utilizing the new technology, the initial appointment for a patient receiving the 3D printed eye lasts seconds.
A non-invasive, non-ionizing scan utilizing a modified Optical Coherence Tomography ophthalmic scanner is made that takes 2.4 seconds. This scanner isn't new and is routinely used in hospitals around the world. Once the scan is complete, a color-calibrated photo of the eye is produced and transferred to the Fraunhofer IGD. The Cuttlefish:Eye software can quickly create a 3D printed model to send to the printer hardware.
The 3D prosthesis is then printed by Fit AG, leveraging its years of additive manufacturing experience. When the printing process is complete, the eye is inspected and then polished by experienced ocularists. With a single 3D printer, the annual requirement of around 10,000 prosthetics annually for Europe could be fulfilled.
With anything implanted into the human body, rigorous quality control measures have to be followed. Cuttlefish:Eye software is classified as a Class 1 medical device. Researchers also performed extensive tests for biocompatibility with the 3D printing material. In the UK, the technology was given a letter of approval for clinical trials by the UK Medicines and Healthcare products Regulatory Agency (MHRA).
About 40 patients will be recruited for the clinical trial, each receiving a 3D printed ocular prosthesis. Over the following 12 months, the participants will be examined by qualified clinicians and asked to report their experiences with the new prosthetic. While a single 3D printer could fulfill the annual need for all of Europe, researchers believe that one scanning device per clinic and the deployment of a small number of geographically located 3D printers could meet the entire global demand for 8 million people in need of prosthetic eyes.
Significant research is being conducted around the world into next-generation prosthetic devices. Much of that research is into advanced prosthetic limbs. For example, new research published last summer investigated using magnets to help control bionic limbs. This year also saw researchers create technology to enable a sense of touch for bionic limbs. A sense of touch is critical to allow the user to know how hard to grasp an object without damaging it or dropping it.
Last December, a man afflicted with quadriplegia was able to feed himself for the first time using advanced robotic prosthetic devices and signals taken from his brain using six electrode arrays implanted directly into the brain. In testing, the patient used the brain-machine interface and robotic arms to slice a Twinkie with a knife and feed it to himself with a fork.